
Raymond Mill Airflow Adjustment: Key Requirements for Efficient Milling
2025年5月9日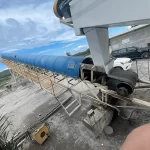
How to Configure a 500t/h Limestone Crushing Production Line: Key Equipment and Design Tips
2025年5月12日
Raymond Mill Airflow Adjustment: Key Requirements for Efficient Milling
2025年5月9日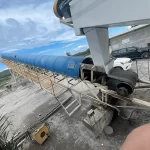
How to Configure a 500t/h Limestone Crushing Production Line: Key Equipment and Design Tips
2025年5月12日Blog
Differences Between Ball Mill and Rod Mill: Structure, Application, and Performance Explained
Differences Between Ball Mill and Rod Mill
Ball mills and rod mills are commonly used crushing equipment, widely applied in industries such as mining, building materials, and chemicals. Although their goal is to crush raw materials into the desired fine particles, there are some obvious differences in their structure, working principles, and applications.
Firstly, a ball mill is a device that uses steel balls as the grinding medium. Its main components include a drum, feeding device, discharging device, motor, and transmission system. When the ball mill operates, the drum rotates at a set speed and moves axially in the horizontal direction. During the grinding process, raw materials are fed into the drum, and as it rotates, the steel balls roll, impact, and grind the materials, achieving the desired fineness.
In contrast, a rod mill uses steel rods as the grinding medium. Unlike the ball mill, the drum of the rod mill is usually straight and is filled with a specific quantity of steel rods. When the rod mill begins operation, the drum rotates at a fixed speed, causing the steel rods to tumble and sway inside. The raw materials are gradually crushed under the impact and grinding action of the rods.
Although both ball mills and rod mills are types of dry grinding equipment, their working principles differ slightly. In a ball mill, the impact and friction of the grinding media are more significant, making it more suitable for fine grinding and uniform mixing of materials. The rod mill, on the other hand, is more appropriate for coarse grinding of hard materials and can provide selective grinding to a certain extent—that is, it allows control over the production of fine particles based on the requirements.
Moreover, the application scopes of ball mills and rod mills also differ. Ball mills are widely used in the processing of metallic and non-metallic ores, construction materials, chemicals, and more. They are suitable for fine grinding and mixing of various ores and materials. Rod mills are mainly used in ferrous and non-ferrous metal beneficiation plants and in other situations that require coarse crushing of hard materials.
In addition to differences in structure, working principle, and application, ball mills and rod mills also differ in other aspects:
- Grinding Effect: Due to the nature of the steel balls, ball mills typically achieve finer grinding results. The impact and friction among the balls make materials easier to break down and refine. The steel rods in rod mills are larger, so the grinding result tends to be coarser.
- Energy Consumption: Ball mills and rod mills also differ in energy consumption. The contact area between steel balls is larger, resulting in higher friction losses and energy consumption in ball mills. The smaller contact area between rods means rod mills consume less energy.
- Maintenance and Operation: Maintenance and operation also differ. Ball mills require regular inspection and replacement of worn steel balls, while rod mills need monitoring and replacement of worn steel rods. Additionally, rod mills are simpler to operate—mainly involving control of drum speed—whereas ball mills require more parameter adjustments and operational oversight.
- Material Suitability: Due to the difference in grinding media, ball mills and rod mills have varying adaptability to materials. Ball mills are suitable for a broader range of materials, especially those with lower hardness. Rod mills are more suitable for handling harder materials.
In conclusion, ball mills and rod mills have distinct differences in structure, working principle, application scope, grinding performance, energy consumption, maintenance, operation, and material adaptability. Choosing the appropriate grinding equipment should be based on the specific properties of the materials and production requirements, making a rational selection based on actual needs.
Need help choosing between ball mill and rod mill for your production line? Contact our experts now for a free consultation and solution design.
Frequently Asked Questions (FAQ)
Recommend Equipment
Solutions
Company Case
Request a Quote
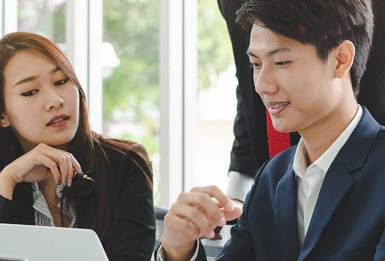