Blog
What Is the Ideal Ball Mill Discharge Fineness for Optimal Production?
This article explores the relationship between ball mill output and powder fineness in industries like cement and chemicals. While finer powder is often desired, it’s not always better. Overgrinding can lead to loss of valuable minerals, increased costs, and lower efficiency. Conversely, too coarse a grind impacts separation processes. The key is to find a balance, controlling fineness to optimize both product quality and production efficiency. Proper operation and material consideration are also vital for maximizing output.
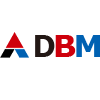
What Are the Components of a Sand and Gravel Production Line?
This article details the components of a sand and gravel production line, which include feeding, crushing, sand making, screening, and conveying stages. Key equipment includes vibrating feeders, jaw and cone crushers, impact crushers, sand making machines, vibrating screens, and belt conveyors. Each stage plays a crucial role in transforming raw materials into finished aggregates, ensuring a smooth and efficient production process.
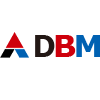
What Is the Difference Between a Sand Making Machine and a Crusher?
This article outlines the key differences between sand making machines and crushers, focusing on five main aspects: equipment type, application field, crushing stage, feed size, and finished product size. Sand making machines, a type of vertical shaft impact crusher, are used for medium and fine crushing, primarily in sand production for construction. Crushers, including jaw, cone, impact, and mobile crushers, handle larger feed sizes and are used for primary crushing of medium-hard materials. Crushers produce larger finished products, while sand making machines generate finer sand, typically under 5 mm, meeting construction standards. The article emphasizes the distinct yet complementary roles of these machines in the sand and gravel production process.
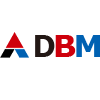
Working Principle of Cone Crusher
This article introduces the cone crusher, a highly efficient crushing machine optimized for strong crushing capacity, intelligent operation, and low operating costs. It excels in medium and fine crushing of hard rocks, producing uniform sand and aggregates. Widely used in metallurgy, construction, road building, and chemical engineering, the cone crusher offers various specifications and models. The article explains its operation, where rocks are crushed between a mantle and bowl liner, undergoing multiple compressions until small enough to be discharged. The cone crusher is praised for its powerful performance, intelligent features, and competitive pricing, making it a popular choice for various industries.
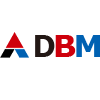
What processes are required to configure a sand and gravel aggregate production line?
This article outlines the essential processes and equipment configuration for setting up a sand and gravel aggregate production line. It highlights the importance of each stage, from feeding and coarse crushing to medium crushing, shaping, and final screening. The article emphasizes the use of jaw crushers for coarse crushing, cone crushers for medium crushing, and vertical shaft impact crushers for shaping and sand making. It also mentions the role of pre-screening in optimizing the process and the flexibility offered by a well-designed system. The article concludes by offering customized equipment configuration plans tailored to specific production needs, whether for hard or soft rock crushing, and for mobile or fixed production setups.
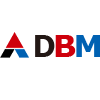