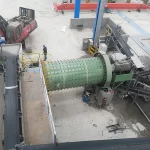
Differences Between Ball Mill and Rod Mill: Structure, Application, and Performance Explained
2025年5月9日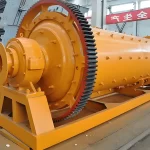
What Is a Ball Mill? Types, Applications, and Working Principle Explained
2025年5月12日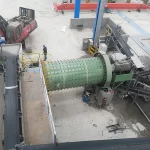
Differences Between Ball Mill and Rod Mill: Structure, Application, and Performance Explained
2025年5月9日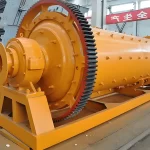
What Is a Ball Mill? Types, Applications, and Working Principle Explained
2025年5月12日Blog
How to Configure a 500t/h Limestone Crushing Production Line: Key Equipment and Design Tips
Limestone crushing production line
Limestone is a common raw material used in construction, with calcite as its primary mineral component. The mineral has fine particles, a smooth surface, and comes in a variety of colors including black, gray, white, yellow, and brown. Limestone is widely used in building materials and is also a crucial raw material in many industries.
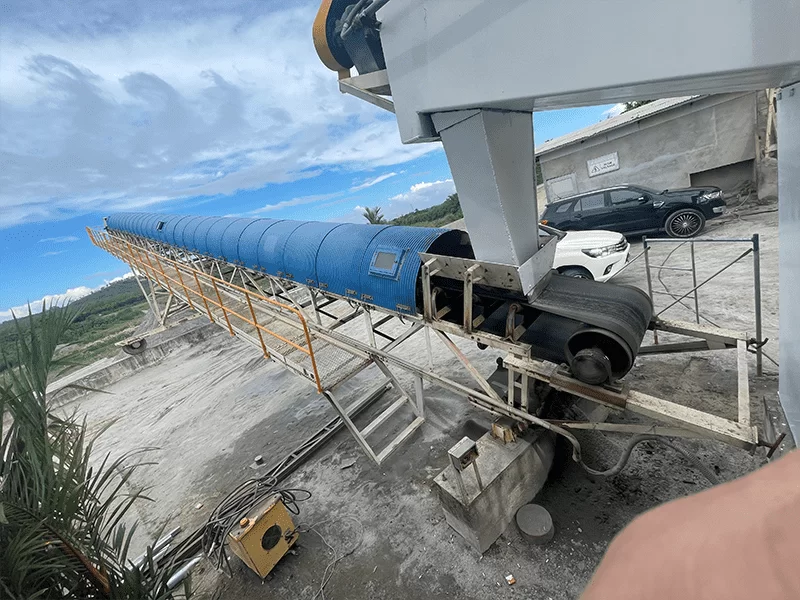
Below is a brief overview of a configuration plan for a 500 tons-per-hour limestone production line:
- Raw Material Storage: To ensure a production capacity of 500 tons per hour, the raw material storage must be able to hold materials from approximately 12 trucks and provide a continuous feed for production.
- Vibrating Feeder: A vibrating feeder, typically a 6-meter long and 1.3-meter wide variable-frequency bar feeder, is used to remove soil and perform preliminary screening.
- Primary Jaw Crusher: The jaw crusher should have a capacity of 500–600 tons per hour. Commonly used models include the 1100×1200 or 950×1250 jaw crushers.
- Impact Crusher: Due to the soft nature of limestone, impact crushers are typically used for medium and fine crushing. For a 500 t/h capacity, two PFQ1315 impact crushers or one 1520 model can be selected.
- Vibrating Screens: Typically, three sets of 2760 vibrating screens are used for inspection and final screening.
- Belt Conveyors: Belt conveyors are used to connect different equipment units and establish a complete production line.
This is the basic configuration of a limestone production line. Additional equipment can be included based on specific production requirements—such as different quantities of sand making machines—to further shape the product and enhance its added value. Depending on market demands, producing high-quality manufactured sand can also improve overall production efficiency.
Notes:
- Material that is not fully crushed in the jaw crusher should be returned for re-crushing. This not only reduces power consumption but also ensures continuous and stable production, thereby maintaining production line efficiency.
- It is recommended that the transfer station have a storage area of 3,000 square meters.
- Environmental protection measures should be implemented after the main production line is built. If a dry process is used, the entire system should be sealed and ventilated. If a wet process is used, spray systems and wastewater treatment should be employed to ensure environmental compliance.
为Looking to set up a 500t/h limestone crushing production line? Contact Dingbo Machinery for custom design and expert support.
Frequently Asked Questions (FAQ)
Recommend Equipment
Solutions
Company Case
Request a Quote
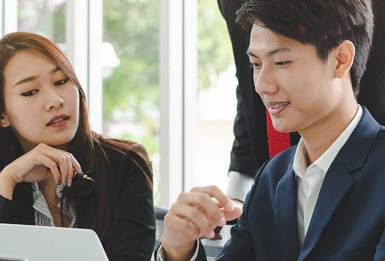